Wind Turbine Maintenance App
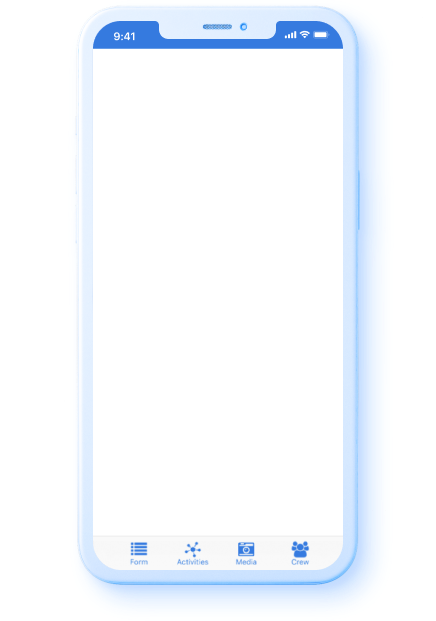
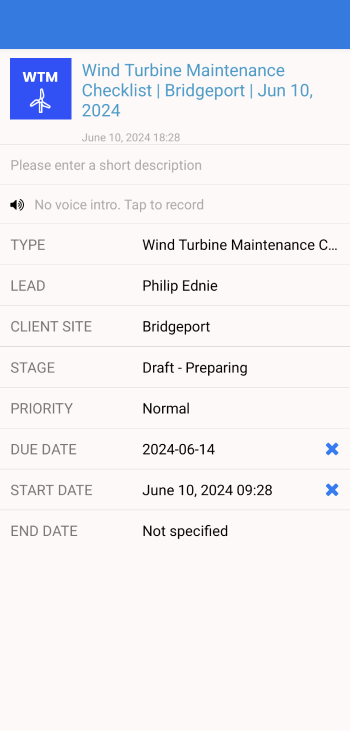
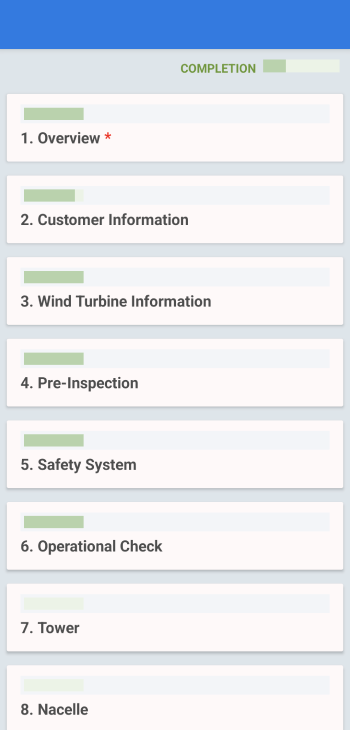
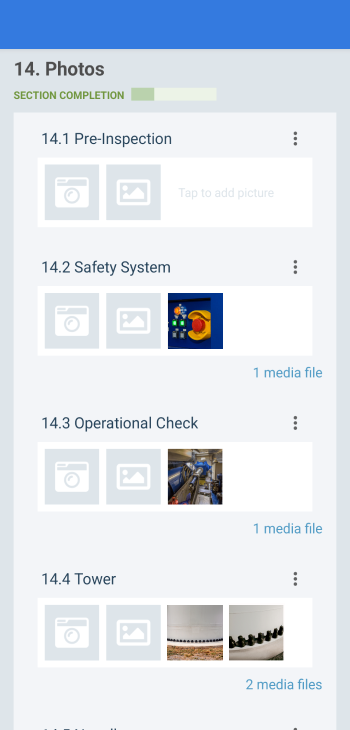
Take the Next Steps to Learn How Scoop Can Help Your Business
Webinars & Product Videos
Book a 1:1 Demo & Free Consultation
Get the Wind Turbine Maintenance Checklist
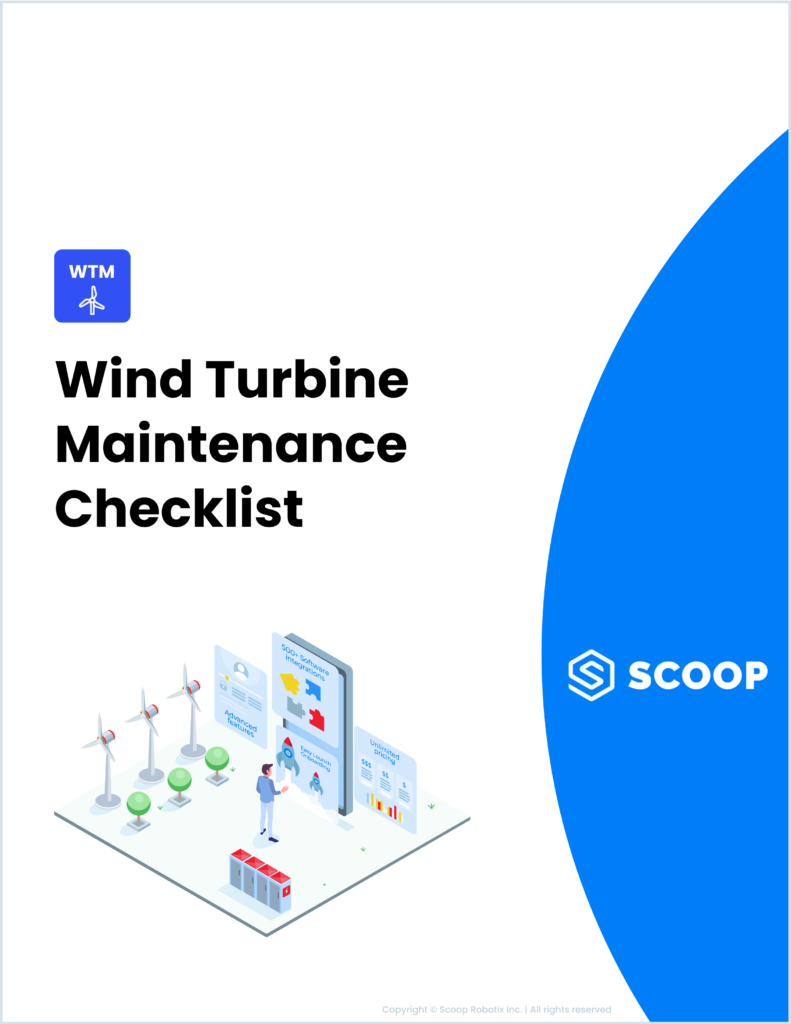
Field Work App FAQs
Wind turbine maintenance involves regular inspections, servicing, and repairs to ensure optimal performance and safety. This process includes a thorough examination of all mechanical, electrical, and structural components. By systematically checking these elements, maintenance teams can identify and address potential issues before they lead to significant problems. This proactive approach helps prevent unexpected failures and extends the turbine’s lifespan, ensuring continuous and efficient operation.
Regular maintenance of wind turbines is important to ensure efficient and safe operation, minimize breakdowns, and extend the turbine’s lifespan. It helps in early detection of potential issues, reducing costly repairs and downtime. Proper maintenance maximizes energy production by keeping components like blades, gearbox, generator, and control systems in optimal condition. This proactive approach ensures reliability and longevity, ultimately contributing to the cost-effectiveness and sustainability of wind energy.
Key components inspected in a wind turbine maintenance checklist include blades, gearbox, generator, and nacelle. Blades are checked for damage, wear, and erosion. The gearbox is inspected for oil levels, leaks, and mechanical issues. The generator’s electrical components are monitored for proper function. The nacelle, which houses critical components, is inspected for overall integrity and proper operation. Additionally, bolts and fasteners are tightened, and lubrication of moving parts is ensured to maintain optimal performance and safety.
Wind turbines should be inspected and maintained regularly to ensure optimal performance and safety. Preventive maintenance, including visual inspections and basic servicing, is typically conducted semi-annually or annually. Comprehensive inspections, which involve detailed checks of key components such as blades, gearbox, generator, and nacelle, are usually performed annually. Additionally, condition monitoring systems continuously track the turbine’s performance, allowing for predictive maintenance and timely interventions as needed. This regular schedule helps in early detection of potential issues, reducing the risk of costly repairs and downtime.