Whether it’s stepping up voltage to tie into a transmission grid, or stepping it down for use on-site, transformers are a core component in the design of many sizable solar PV systems. However, the transformer lead time is often the longest delivery lead time of any system component, so require special attention to how you source them. Today, we’re taking a look at the transformer lead time for solar markets with some insight from Mac Spiller, Director of Sales at Maddox Industrial Transformer, an Inc. 500-ranked supplier to EPCs and commercial & industrial customers, including a large number of solar projects.
What’s driving transformer lead times for solar projects?
Demand for both power and distribution transformers is driven by several booming sectors of the economy. Maddox sees strong ongoing demand from traditional sectors like oil, gas, and utilities, as well as emerging energy-intensive industries like cryptocurrency mining and medicinal cannabis. Many manufacturers have contracts with utilities, and so production priority goes to them and their large order volume. All this growth means that solar companies who need one transformer for a project are usually left at the bottom of the pecking order.
In peak seasons US factories typically take about 20 weeks to build and deliver a new 3-phase transformer.
Transformer lead time can vary by the time of year; in peak seasons US factories typically take about 20 weeks to build and deliver a new 3-phase transformer. 10-12 weeks is a typical lead time during slow seasons.
Mac explains that this timeline is problematic for many solar projects: “Lead times on inverters and other equipment is typically closer to 8 weeks. So, projects which could be completed faster are stretched out because of the transformer ‘long pole’ in delivering materials to the site,” he says.
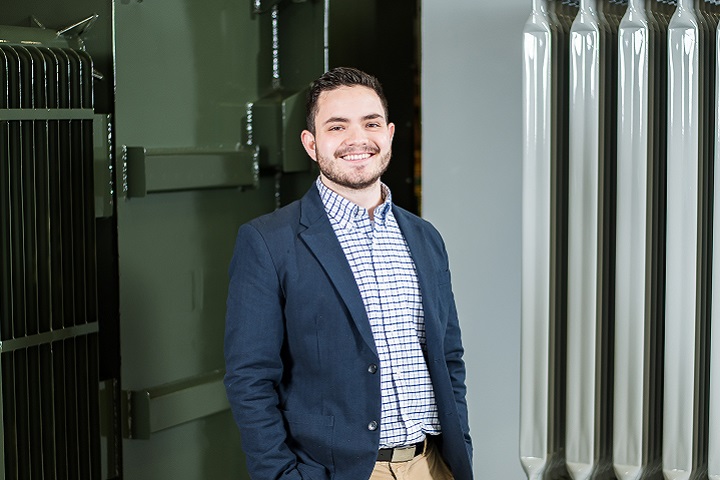
In other industries, reconditioned transformers provide a faster delivery alternative to buying new. Transformers are a fairly ‘static’ technology, so a 10-year old unit is not dramatically different from a new one—it’s either working or it’s not.
About half of the units Maddox sells are reconditioned, often purchased when manufacturing plans are shut down. But reconditioned units are usually not an option for solar installations because of the stipulations attached to government incentives.
“When there’s stress on the supply chain many of our customers can look to used equipment,” says Mac. “But usually when solar government money is involved, the contract says the equipment has to be new and the factory has to be UL listed.”
Strong global demand is also a factor; most of the large power transformers used in utility-scale projects in the US are sourced from China, which is also supplying stock to the Asia Pacific region. APAC is forecast to emerge as the fastest-growing market for transformers over the next 4 years which will further tighten supply from outside the US.
Maddox plans their capacity schedule specifically so they can fulfill smaller orders and reduce the transformer lead time on solar projects. They maintain dedicated slots in their production schedule that they make available every week. These slots are not behind other orders or subject to factory loading. This allow them to deliver new custom-built pad-mount transformers within 7 weeks, suitable for most of the solar projects they supply.
Certain transformer features are in high demand
Most solar EPCs are purchasing liquid-filled pad mount transformers and 600 V-class dry type transformers. While the fundamentals of transformer design are not rapidly changing, certain design features are becoming more frequently requested. Mac says that more utilities have started requiring solar installations to include grounding transformers in order to connect to the grid in their service territory. This and other specific design requests further limit the option of using reconditioned units.
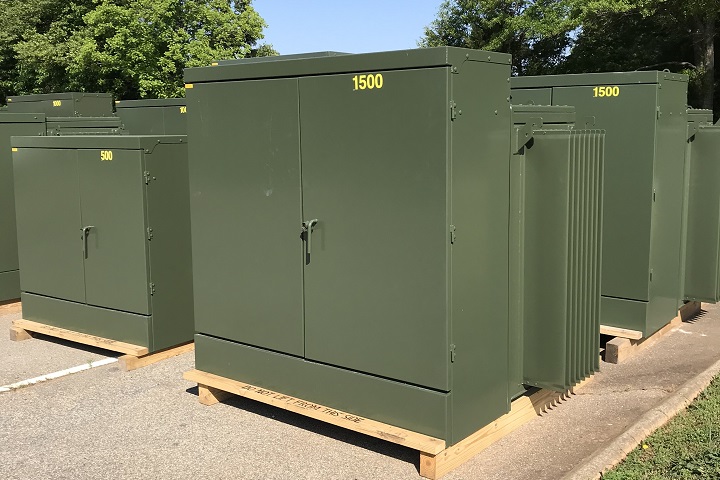
Buyers are also increasingly requesting transformers that use FR3, a high-flashpoint, more environmentally friendly fluid. This is particularly common when engineers are designing solar farms near water sources, where concerns about oil spills are heightened. This adds about 20% to the total cost of the transformer, but it mitigates risk to the environment and usually results in a higher power factor.
Electrostatic shielding is another popular feature in transformers installed at solar power plants. These models incorporate shielding between the high and low voltage coils, which reduces the amount of voltage distortion, and delivers cleaner power.
From a servicing perspective, many buyers are requesting pad mounted designs that bring certain controls outside of the primary cabinet into a secondary, lockable box. This includes liquid drains, thermometers, pressure gauges, liquid level gauges, bayonette fusing, and the load break switch. Having these controls outside of the main cabinet makes for a much safer experience for field technicians servicing the units.
Getting the transformers on site faster
In addition to keeping production slots open each week, Maddox also employs several other techniques to help keep lead times down for solar projects. The firm keeps most common designs in stock at all times at both their locations. This allows them to deliver suitable transformers quickly to get projects with very tight deadlines to a mechanically complete status; they can then be swapped out for the unit built to the exact requested specification when it is finished.
“We know that managing construction projects is difficult… A lot of times we end up storing transformers for solar contractors until they can actually take delivery on site.” – Mac Spiller, Director of Sales, Maddox Industrial Transformer
Mac says that Maddox’s familiarity with solar projects is a big part of the ease of doing business with them.
“We’re just used to working with solar EPCs,” he says. “We understand that payment terms have to be flexible. Often times they’re working with payment schedules that don’t allow them to pay up front for equipment, and maybe not net 30 or even net 60, so we work with them.”
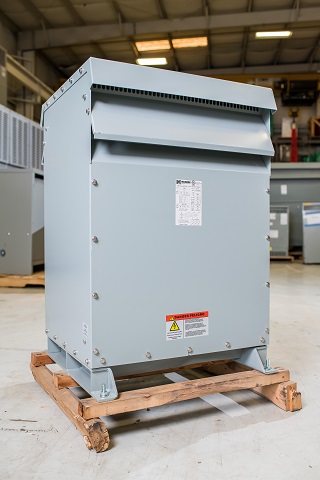
“Storage flexibility is also important for solar EPCs,” he continues. “We know know that managing construction projects is difficult and things don’t always hit their deadlines, so a lot of times we end up storing transformers for solar contractors until they can actually take delivery on site. Many of them have to rent cranes, which makes the delivery windows quite time sensitive.”
Maddox is one of the fastest growing companies in the US, and has recently opened a second manufacturing and storage facility in Battle Ground, WA, in addition to its corporate headquarters in Greenville, SC. Learn more about their product line and services at http://www.maddoxtransformer.com
Scoop Solar is helping renewables businesses streamline their solar operations. We work with companies around the world and the Scoop platform has executed projects at over 25,000 client sites. Contact us to learn more.
Solar Panel Transformer FAQ
What is a transformer for solar panels?
Transformers are a type of technology used in many industries to increase energy efficiency and lower energy costs. Transformers are designed to convert electrical energy from one form to another, such as from AC to DC. This helps save on energy costs by using less power to produce the same level of output. Understanding how Transformers work can help you take advantage of their technology in your own home or business.